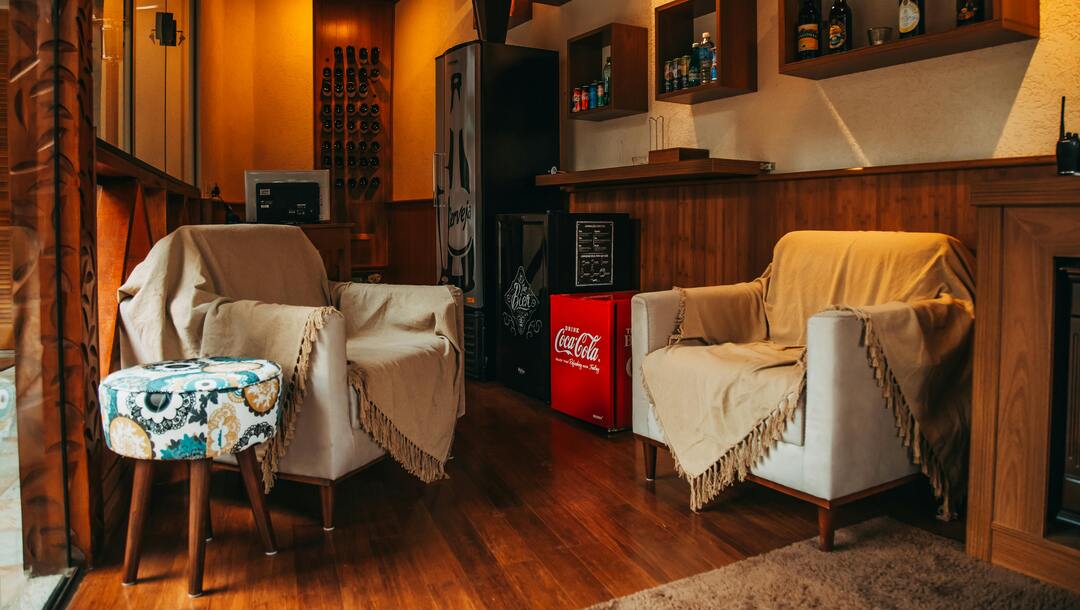
How Engineered Wood Flooring is Made?
June 12, 2024Craftsman Tom, in a timber-rich town, made Engineered Wood Flooring. He selected quality timber, cut it into layers for stability, and bonded them with heat and pressure. His floors, admired for their quality and elegance, symbolized his craftsmanship.
Imagine stepping onto a floor that marries the beauty of natural wood with the resilience of modern engineering. Engineered wood flooring is more than just a design choice; it's a material innovation that's reshaping how we think about durability and style in our living spaces. From its layered construction to the variety of available wood species, engineered wood flooring offers a unique blend of practicality and aesthetic appeal. This article delves into the intricacies of how engineered wood flooring is crafted, the varieties that exist, and the advantages it holds over traditional hardwood flooring, ensuring you have all the information you need to understand this modern staple in home design.
What is Engineered Wood Flooring?
Engineered wood flooring represents a popular choice among homeowners who appreciate the look of real wooden floor but desire more stability and resistance to environmental changes. Unlike solid wood flooring, which is made from a single piece of wood, engineered wood flooring is constructed of multiple layers, providing enhanced structural integrity.
Definition of Engineered Wood Flooring
Engineered wood flooring is a sophisticated type of wood floor that consists of several plywood layers laminated together to form each board. The top layer, often referred to as the wear layer or lamella, gives the appearance of natural wood and is actually a thin slice of solid hardwood layer. This layer provides the natural beauty and uniqueness found in solid wood flooring, available in a broad range of wood species, including both domestic hardwoods and exotic woods.
Beneath the lamella is the core layer, typically composed of plywood, high-density fibreboard (HDF), or multiple layers of wood veneers. Plywood is a common choice because its layers of wood fibres, oriented in different directions, confer additional stability to the floorboards.
The engineered boards are typically milled with precision to have a tongue-and-groove profile which ensures a snug and even fit during installation. This structure makes engineered wood a practical and versatile option, as it minimizes the shifting and cupping that can occur with solid wood floors in response to ambient humidity and temperature changes.
Overall, engineered wood flooring offers the authenticity of real wood flooring, but with greater resilience and often comes at a lower cost per square foot compared to solid wood floors. It's a preferred material for both commercial and residential projects due to its beauty, versatility, and durability.
The Construction of Engineered Wood Flooring
Engineered wood flooring is a multi-layered product designed to provide enhanced stability and resistance to environmental changes than traditional solid wood floors. At the heart of its construction is the top layer of solid hardwood, which is bonded to a plywood base, creating a stable and strong board.
The Middle Layer: High-Density Fibreboard (HDF)
Engineered wood flooring can also incorporate a middle layer made of High-Density Fibreboard (HDF). HDF is selected for its impact resilience, contributing to the floor's durability. This core material is created by mixing wood chips with resin and compressing them under high pressure to form a rigid and sturdy base.
HDF cores enhance the overall strength and stability of the wooden flooring, providing a reliable foundation that supports the lustrous hardwood veneer on top. Additionally, the use of HDF can render the finished product more cost-effective without compromising on the floor's quality or performance.
However, due to its construction, HDF is not recommended for areas subject to high moisture, as it can be more susceptible to swelling and damage when exposed to excessive water. When choosing engineered wood flooring for such environments, alternatives like plywood may be a better fit.
The Layers of Wood Veneers
The layered structure of engineered wood flooring is integral to its design, featuring three main components: the top hardwood veneer, the core layer for structural stability, and a backing layer that ensures an even overall construction.
The Hardwood Veneer
The top hardwood veneer is not just for looks; its real hardwood construction offers the look and feel of solid wood floors with the practical benefits of engineered flooring. The uniform thickness of the veneer layer determines how often the floor can be refinished, with thicker layers extending the product's longevity.
Core and Backing Layers
The core layer, nestled between the hardwood veneer and the stabilizing backing, maintains the floorboard's structural integrity. It cushions against foot traffic and provides a barrier against environmental shifts that can cause lesser quality floors to buckle or gap.
While the high-density fibreboard is one option for the core layer, wood veneers are also used. Veneers are thin slices of wood, just like the top layer, but stacked in perpendicular layers. This cross-structuring of veneers gives the flooring incredible strength and prevents the natural expansion and contraction that solid wood is prone to.
In summary, engineered wood flooring is not simply a piece of wood but a complex construction of various wood materials providing beauty, durability, and lasting performance for diverse settings.
The Manufacturing Process of Engineered Wood Flooring
Engineered wood flooring is a sophisticated composite that combines the natural beauty of solid wood with the stability and resilience of intelligent engineering. It is the result of a multi-step manufacturing process that ensures each piece of flooring is both strong and aesthetically pleasing. This flooring solution is designed for versatility, sporting a top layer of genuine hardwood attached to a robust core, which can be composed of high-density fiberboard (HDF) or plywood, and a bottom layer that is often similar to the core layer.
Step 1: Cutting the Logs
The journey to creating engineered wood flooring begins with the meticulous selection of quality logs. Each log is chosen based on its wood species, which ultimately influences the color, grain, and overall aesthetic of the finished product. These logs are the raw materials that will be crafted into the top hardwood veneer layer of the engineered flooring. High standards and quality control measures are strictly applied during this initial phase to secure the desired caliber of the final flooring product.
Step 2: Processing the Wood Chips
Subsequent to log selection, the wood is processed into chips and then into veneers, which are thin, uniform slices approximately 2mm thick. These are what make up the core layer when bonded together using high-pressure presses. Producing a single core board with a thickness ranging from 14mm to 15mm, this step is critical for achieving the stability and quality that characterize the best-engineered wood boards. After the hardwood top layer is affixed to the plywood base, the composite boards are transferred to drying chambers to ensure precise moisture content, optimizing their stability and longevity.
Step 3: Creating the Wood Fibers
During this phase, wood fibers are carefully prepared for integration into the softwood core of the flooring. Multiple layers of thin wooden planks are arranged cross-grain and securely glued using professional equipment to guarantee a seamless strong bond. This arranged layering rectifies the natural propensity of wood to expand and contract, thereby bolstering the floor's robustness. By using hot-pressing equipment and precise monitoring, the engineered wood flooring is fortified, ensuring its dimensional stability and exceptional quality.
Step 4: Producing the High-Density Fibreboard
For engineered wood floors that utilize an HDF core, the production process involves mixing fine wood particles with adhesives to create a strong, dense board. The mixture is then compressed under intense pressure to form the HDF, which lends significant strength and resilience to the overall construction types of the board. Despite the durability advantages of the HDF core, its use is typically circumvented in areas prone to high moisture due to the potential for water damage.
Step 5: Constructing the Layers of Wood Veneers
At this stage, the thin slices of real hardwood that form the top layer veneer are bonded to the constructed core layer using powerful adhesives and high-pressure presses. The thickness of this hardwood veneer varies, with thicker veneers affording the opportunity for additional refinishing over the life of the floor. A backing layer is then applied to the bottom, mirroring the core material, to ensure the board remains flat and stable.
Step 6: Pressing and Bonding the Layers Together
The pressing and bonding of the engineered wood flooring's various layers determine its structural integrity. By using modern adhesives, the hardwood top layer is bonded to the core base, typically made of 14mm or 15mm thick plywood. The different layers are pressed together under controlled conditions to effect a solid bond. After pressing, boards are placed in drying chambers to eliminate any excess moisture, thus guaranteeing the engineered wood’s quality and dimensional stability.
Step 7: Cutting the Engineered Wood Flooring Boards
After the layers have been pressed and bonded together, the boards are then precisely cut and profiled to ensure uniformity in dimensions and enable proper board-to-board fit during installation. The precise cutting process gives the engineered wood flooring its final dimensions, including the tongue-and-groove edges that facilitate seamless locking between adjacent boards.
Step 8: Finishing the Engineered Wood Flooring
The final step in the manufacturing process involves finishing the engineered wood flooring surface to enhance its aesthetics and durability. Options include oil or lacquered finishes, where oil imbues the wood with richer hues and offers surface protection from scratches, while lacquer creates a glossy, protective layer. The type of wood flooring lacquer finish chosen will greatly influence the engineered wood's final sheen and contribute to the overall aesthetic of the installed floor. Customizations such as sanding, sculpting, and choosing the species of wood allow for a personalized touch, ensuring the flooring complements the desired interior design scheme.
The manufacturing of engineered wood flooring is a truly innovative process that combines the natural elegance of wood with the engineering necessary for modern demands. The result is a high-quality, versatile flooring solution that is both enduring and a testament to the skillful blend of nature and technology.
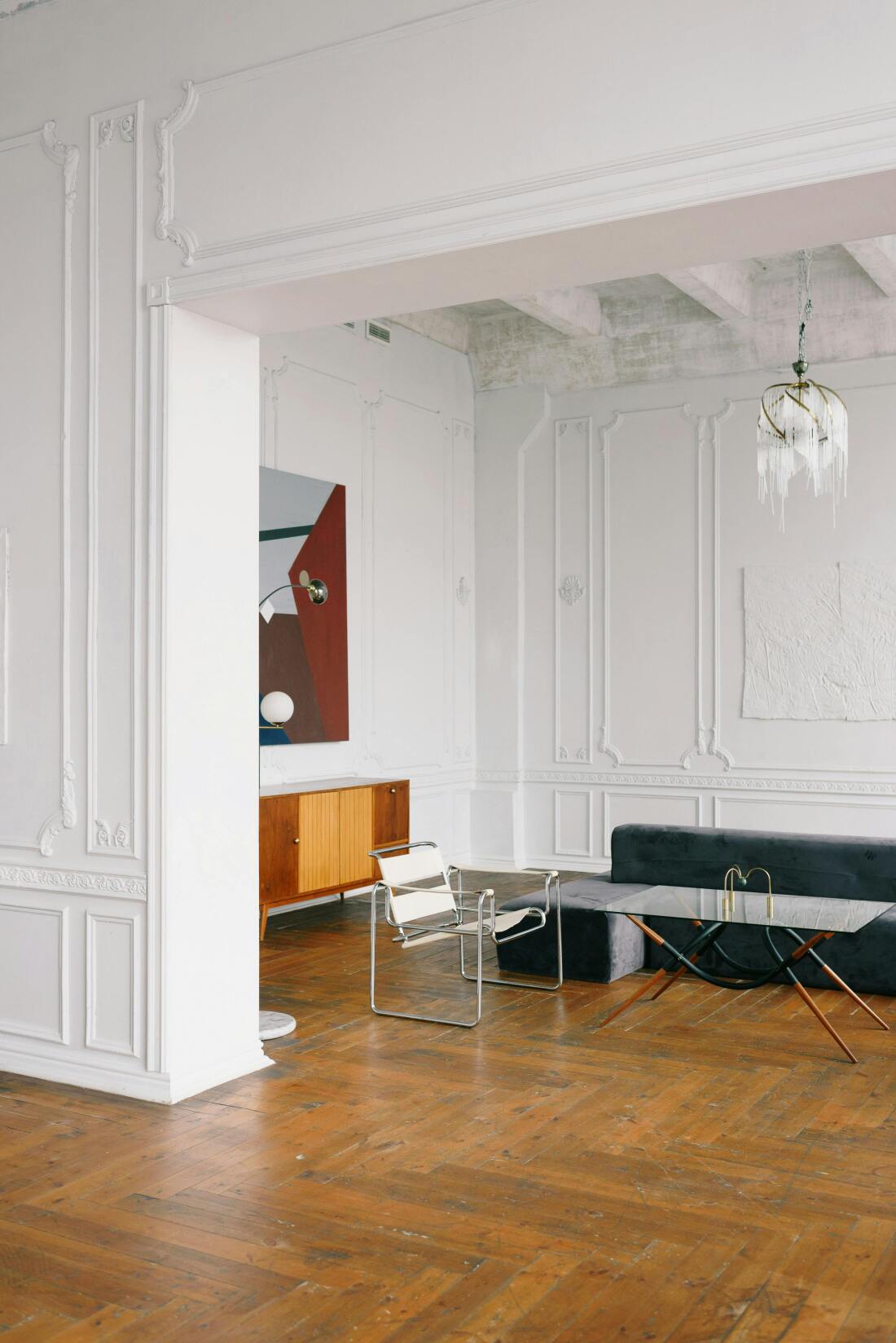
The Variety of Wood Species Used in Engineered Wood Flooring
Engineered wood flooring offers a rich diversity of wood species, each granting a distinctive charm and individuality to this versatile type of flooring. Renowned for their aesthetic appeal, wood types such as oak, maple, hickory, and walnut provide myriad natural hues, grain patterns, and strength characteristics, enhancing both the floor's performance and visual allure. Exotic woods like acacia and teak introduce an international flair, boasting high durability and unique grains that can transform any interior space into a stunning display of natural beauty.
Popular Wood Species for Engineered Wood Flooring
Among the wealth of options, certain wood species stand out as popular favorites for engineered wood flooring. Oak reigns supreme for its hardiness and classic grain patterns, imparting a timeless elegance to homes and commercial spaces alike. Maple, with its subtle grains and lighter color palette, offers a contemporary feel suitable for brightening rooms, while the sturdiness of hickory caters to high-traffic areas with its exceptional resilience. Walnut engineered floors exude luxury, presenting rich, dark tones and intricate graining, delivering an unmistakable air of sophistication to any room they grace.
Exotic Woods for Engineered Wood Flooring
Exotic woods such as cherry and maple, though often tagged as unconventional, are gaining ground in the market, thanks to their rich character and rare beauty. Cherry, famed for its vibrant red and brown hues, underscores warmth and hospitality, making it an ideal option to create a cozy ambiance. The uniqueness of its grain adds to cherry's draw as an exotic choice. In contrast, maple tends toward the traditional, offering a light, creamy look that marries well with a multitude of decor styles. Its exceptional durability secures maple's status alongside oak as a flooring that couples elegance with lasting performance. These exotic woods present an array of distinct color variations and wood patterns, broadening the horizon for homeowners and designers to articulate their creative visions through their flooring selections.
Advantages of Engineered Wood Flooring
Engineered wood flooring stands out as a remarkably stable and durable alternative to traditional solid wood flooring. Its ingenious ply construction combines multiple layers of wood veneers, contributing to a robust structure that resists shrinking, warping, and buckling. This resilience is particularly valuable in regions experiencing wide climatic swings, as engineered floors maintain their form and dimension despite environmental changes. Furthermore, modern advancements such as click systems simplify installation, enabling homeowners to undertake DIY projects without the need for professional help, thus saving on labor costs.
This type of flooring boasts a lengthy lifespan, often exceeding 30 years with the right care and maintenance, which speaks to its lasting appeal and cost-effectiveness. Engineered wood planks are generally wider and thinner than their solid wood counterparts, offering an expansive array of design options to fit diverse spaces and aesthetic preferences. Eco-conscious consumers will also appreciate engineered wood flooring for its sustainable qualities. Not only does it use less slow-growth hardwood, reducing the impact on forests, but it often incorporates materials like high-density fibreboard and faster-growing wood species in its core layers, making it an environmentally friendly option for modern building practices.
Durability and Stability
Engineered wood flooring is renowned for its robust nature. Thanks to its design, which typically involves a hardwood layer atop high-density fibreboard or plywood, these floors are less susceptible to the common pitfalls that plague solid woods, such as warping or cupping. The multi-layered approach to engineered wood flooring provides extraordinary stability, ensuring the floor remains flat and intact through humidity swings and temperature shifts.
Such strengths are particularly advantageous in environments like kitchens and bathrooms, where moisture levels can frequently change. Additionally, engineered wood floors can be easily restored to their former glory if the top layer suffers damage. A round of sanding can revitalize the floor’s surface, prolonging the life of the flooring and making it a smart financial and aesthetic investment.
Environmental and Cost Benefits
Engineered wood flooring is not only a practical choice but also an environmentally responsible one. By utilizing a smaller proportion of prized timber species such as Oak for the visible top layer and opting for more abundant woods for the lower strata, engineered floors promote forest conservation and sustainability. This characteristic aligns with rising environmental awareness and the push for greener building materials in residential and commercial construction.
From a cost perspective, engineered wood offers a spectrum of options, generally ranging from $2.50 to $10 per square measure. This affordability, coupled with the advantages of wider boards and compatibility with underfloor heating systems, positions engineered wood as a financially viable alternative to solid wood floors. Furthermore, the integrity of engineered wood flooring is heavily reliant on the quality of adhesives used during production. When manufacturers utilize superior adhesives, the durability and shelf-life of the wood flooring boards are significantly enhanced.
Versatility in Design
One of the standout attributes of engineered wood flooring is its vast design potential. It presents a smorgasbord of colors and finishes — from the natural to the more daring gray and whitewashed tones. Such versatility allows it to align with a multitude of aesthetic directions, from rustic to modern minimalist. Adding to this is an assortment of plank installation patterns, including straight, diagonal, and more intricate designs like herringbone or chevron. These arrangements provide the opportunity for homeowners to infuse their spaces with personalized touches and create striking visual appeal.
The design flexibility engineered floors offer is further emphasized by the wide plank widths and varied lengths available, catering to unique preferences and enhancing the sense of space within a room. Engineered wood delicately balances the classic charm of hardwood with the practicality and stability of its layered construction, delivering a flooring solution that is both eye-catching and enduringly functional for a diverse array of residential and commercial interiors.
Unleash the Beauty & Strength: Engineered Wood Flooring Explained!
Imagine a floor that marries the timeless elegance of natural wood with the resilience of modern engineering.
- Visit our website today!
- Click here and discover your perfect floor today!